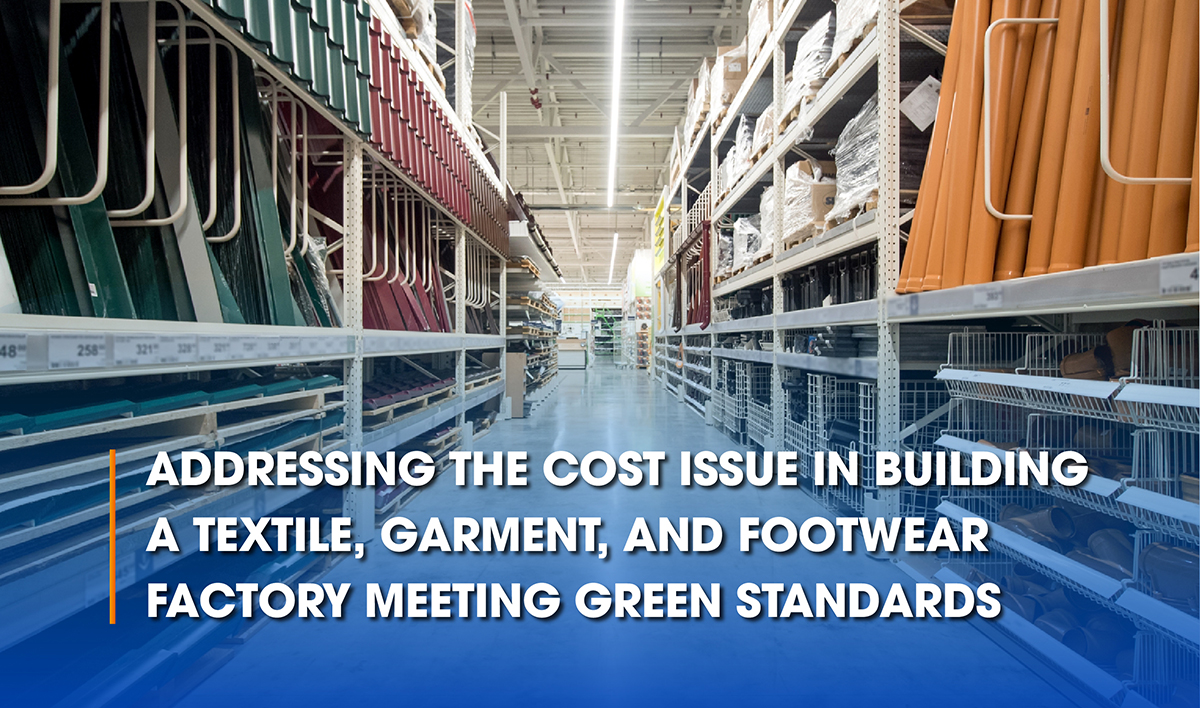
The cost issue is always a tough nut to crack for investors and consulting firms alike. The design is taken into consideration to fulfill the requirements for construction quality, durability and beauty as well as meet the necessary standards without a significant increase in total investment.

Based on many years of experience in consulting and designing several textile, garment, and footwear factories with hundreds of millions of dollars in scale, Mr. Le Duy Khoi, Director of ICC Consultancy, realized that while many local firms are mindful of their budget spending, FDI investors always place a top priority on compliance with regulations and standards, especially social security for their workers.
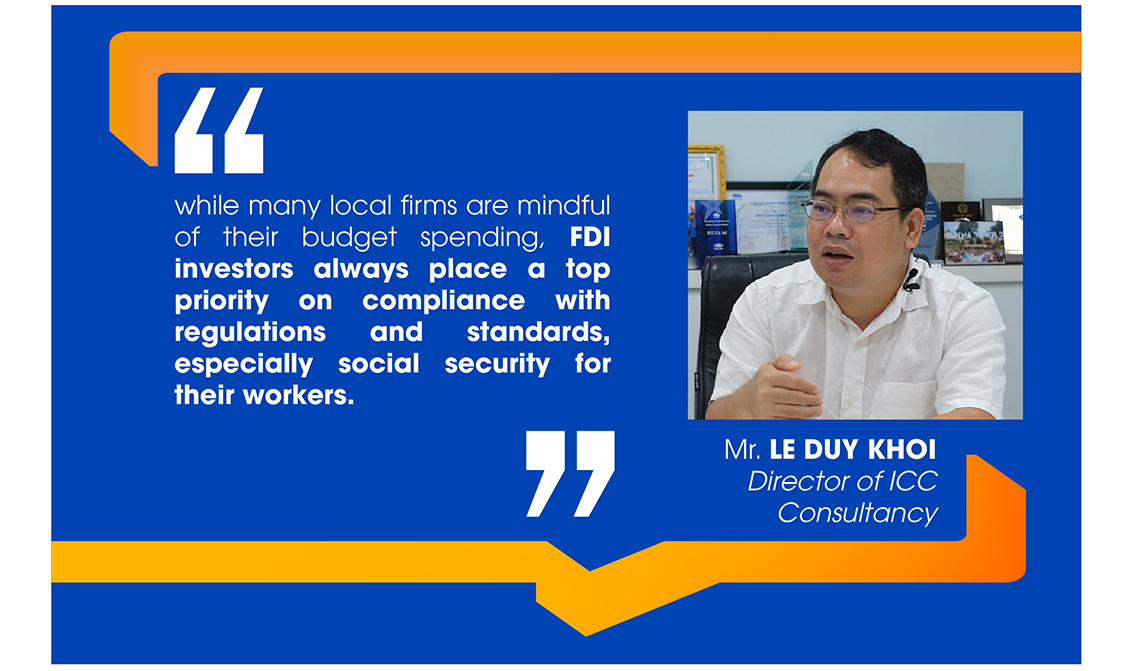
However, multinational corporations have recently imposed new requirements on manufacturers and suppliers of textile, garment, and footwear products. Specifically, there are requirements to meet green standards, energy-saving standards, and even the net zero requirements of some corporations. In addition, propaganda about green buildings has gained traction. While the Vietnam Textile and Apparel Association and the Vietnam Leather, Footwear, and Handbag Association promote propaganda about this issue, the Vietnamese government has made a commitment to the international community to achieve net zero emissions by 2050. As companies have increased awareness of this issue, they are taking steps to study for applications.
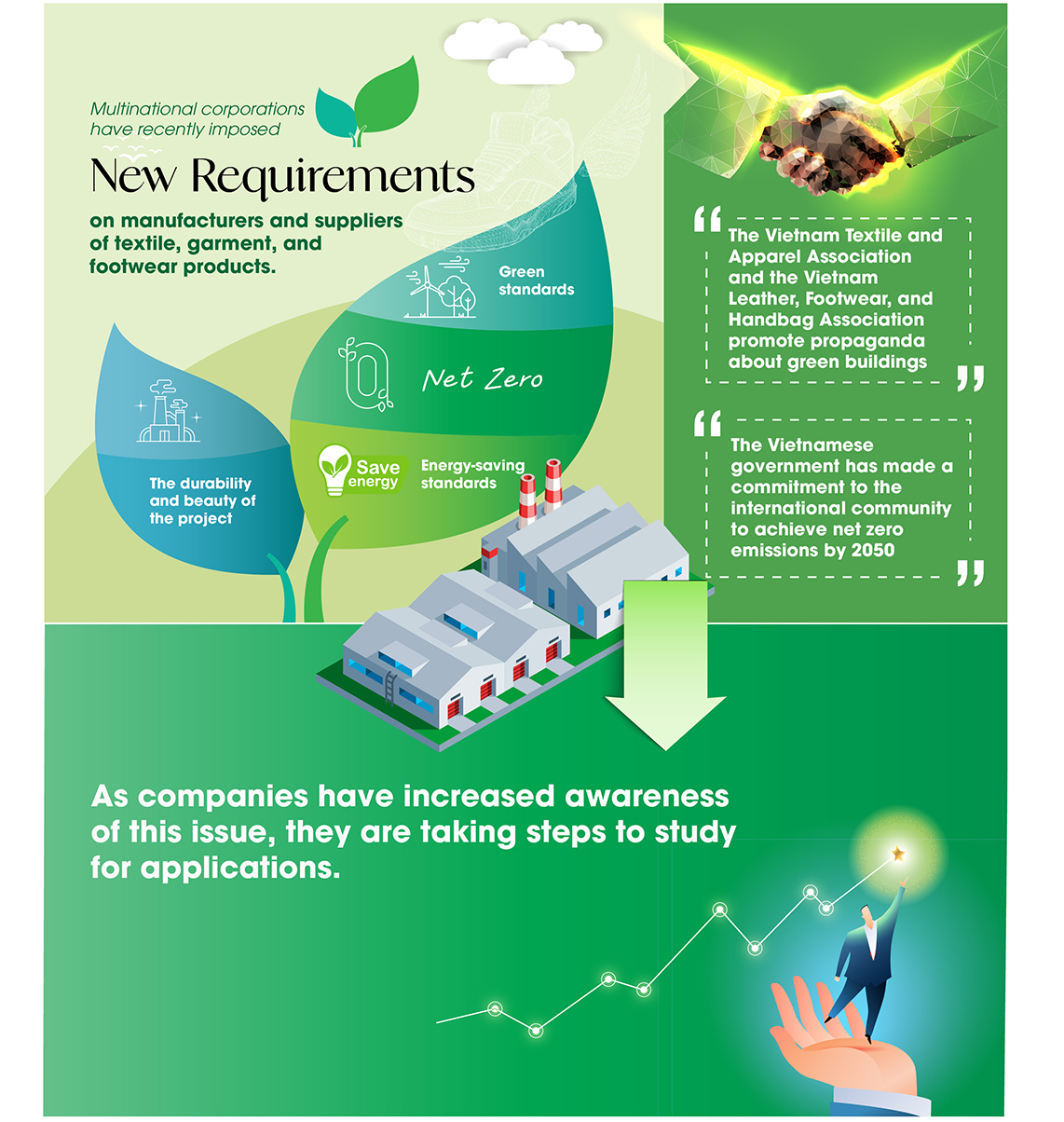
However, the textile, garment, and footwear factories are land- and labor-intensive, so there are some difficulties in applying green standards across many areas.
Alongside fulfilling the requirements of green standards, the durability and beauty of the project are the major concerns for investors. Specifically, a beautiful project will enhance the company’s image, while sustainability will ensure the stable operation of a factory in the long run. When a factory has been in operation for 10 years, removing the roofs for repair and replacement will greatly affect the internal operation and even result in costly expenses.
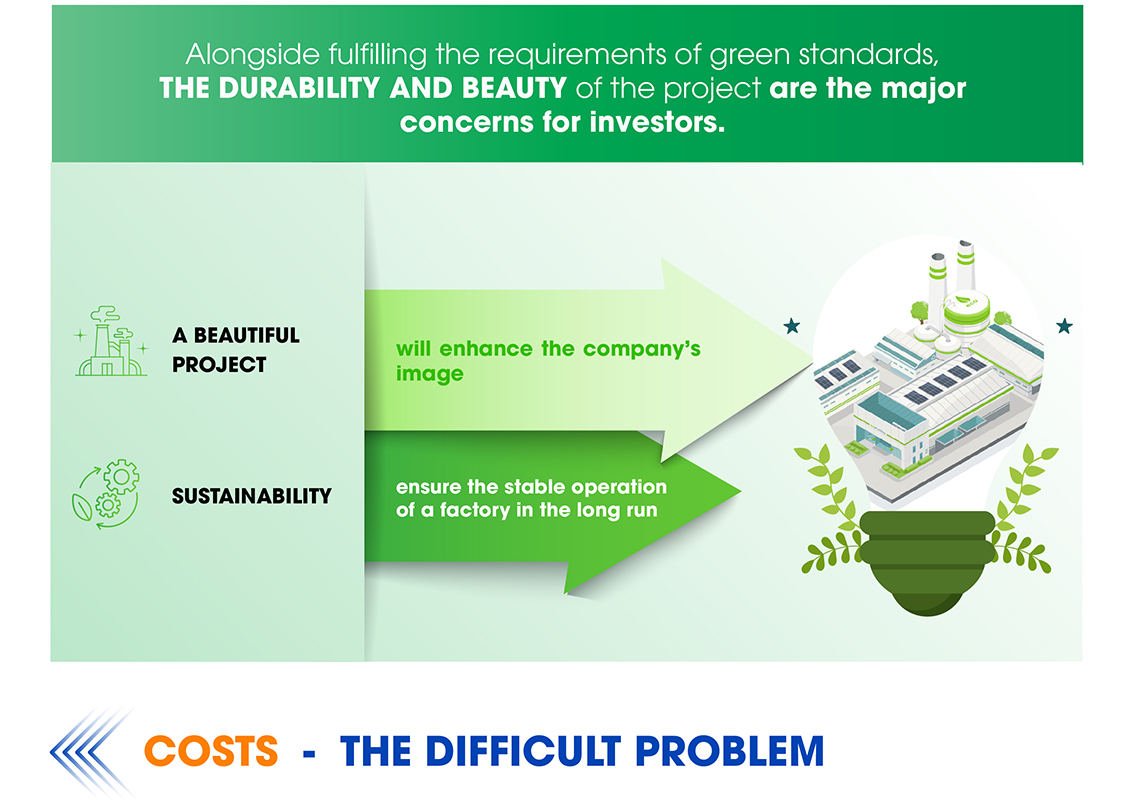
Mr. Le Duy Khoi revealed that the costs of green building projects are on a downward trend due to changes in technology and raw material production costs. “If we compare the normal textile, garment, and footwear factories with the LEED-certified ones, the gap is about 3 – 5%. This figure is about 3 – 10% for LEED Silver or Gold and about 10 – 15% for LEED Platinum.”
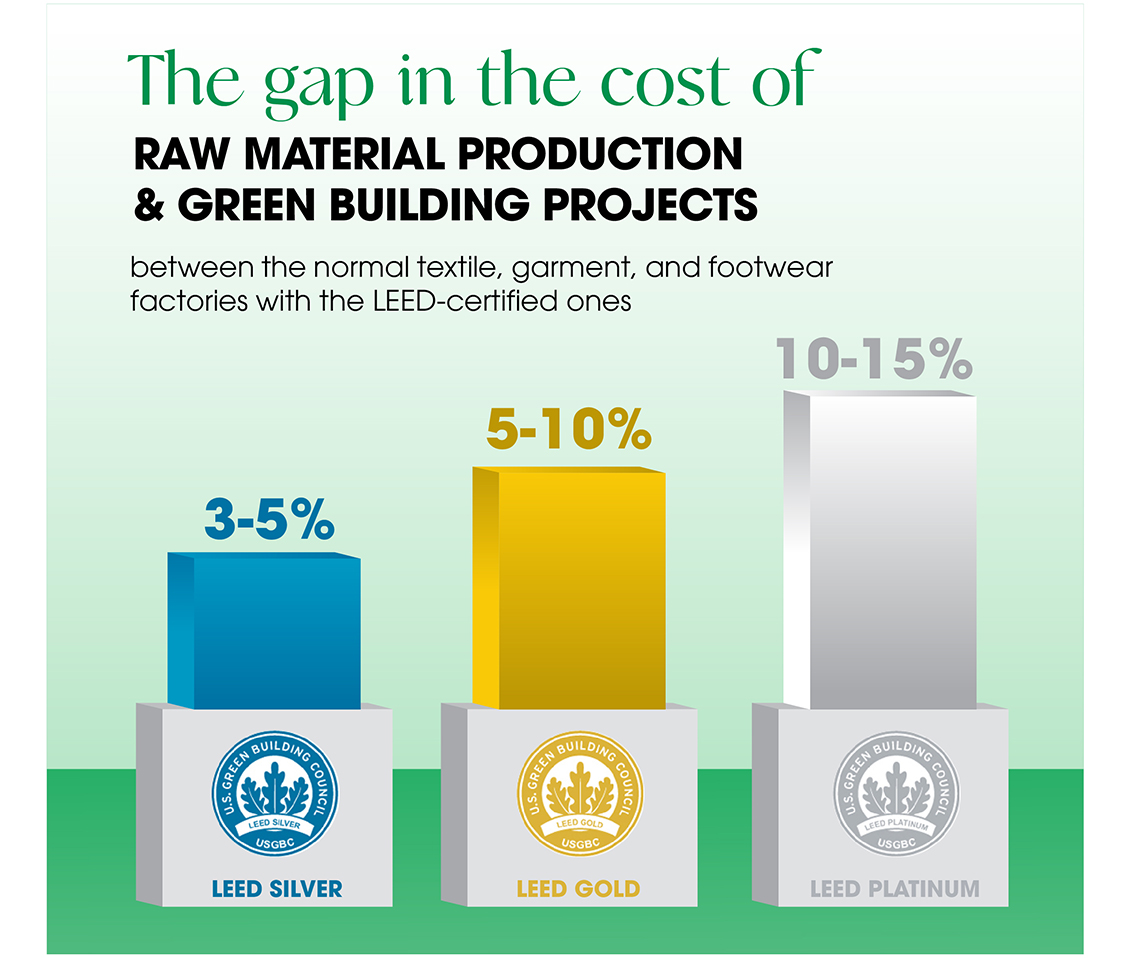
However, as the textile, garment, and footwear project features a huge investment capital, up to hundreds of millions of dollars, only a few percentages can lead to a surge in budget. In addition, the risks of price fluctuations in the market also result in a significant increase in total investment. It is this issue that dampens investors’ confidence.
Nevertheless, according to experts, investors should pay more attention to the long-term investment value than the short-term costs. Being mindful of budgets and delaying renovation and updates later is a misconception, which does more harm than good. According to Mr. Le Duy Khoi, there are many difficulties in renovating an existing factory because new regulations and standards make the renovation more complicated. The renovation costs are huge, sometimes even higher than the new construction. Not to mention that production activities inside the factory will be suspended during the renovation period, affecting the company’s ability to fulfill the orders. The standardization of design and construction right from the beginning is the key to the stable operation of the factory in the future.
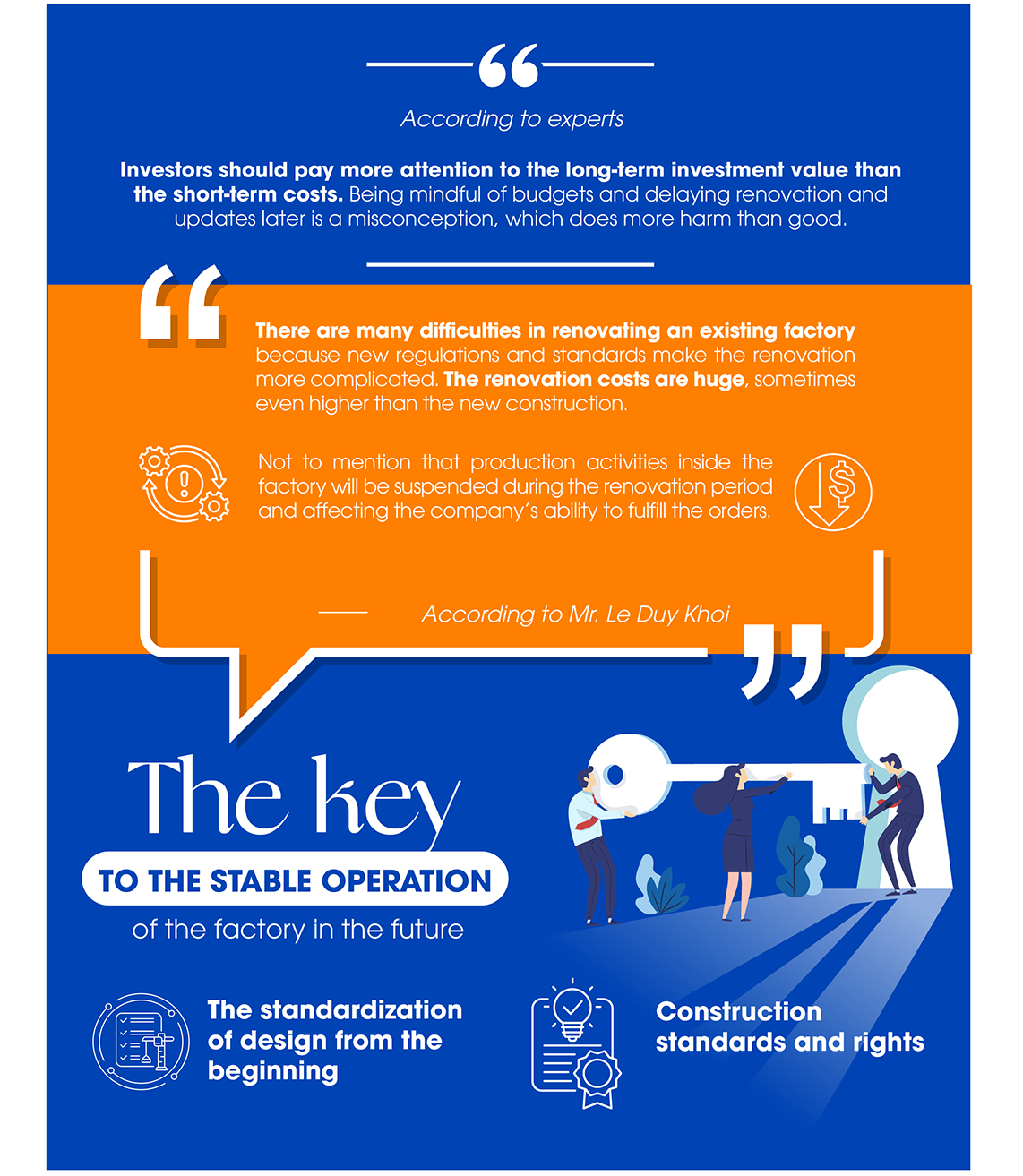
Mr. Le Duy Khoi has also brought attention to factories in areas with a harsh climate and a highly corrosive environment. These projects should opt for products with high plating content. NS BlueScope’s COLORBOND® steel can meet this requirement.
“The reality is that at some factories in operation for over 15 years, NS BlueScope’s steel still maintains its color durability and shows no signs of corrosion,” – Mr. Le Duy Khoi emphasized.

The question raised for most investment projects is how to achieve a balance between financial capability and expected goals. Beautiful, sustainable designs meeting the requirements of regulatory bodies and the soft standards in international markets are the criteria every investor strives for. However, it is challenging to achieve all these goals simultaneously due to the limited budget.
From a consulting perspective, Mr. Le Duy Khoi pointed out some points that investors should do right from the beginning and other points that do not need to be done right away. Instead, investors should do the preparation work to facilitate expansion and improvement in the future. “An open design will help solve this problem,” – Mr. Khoi shared.
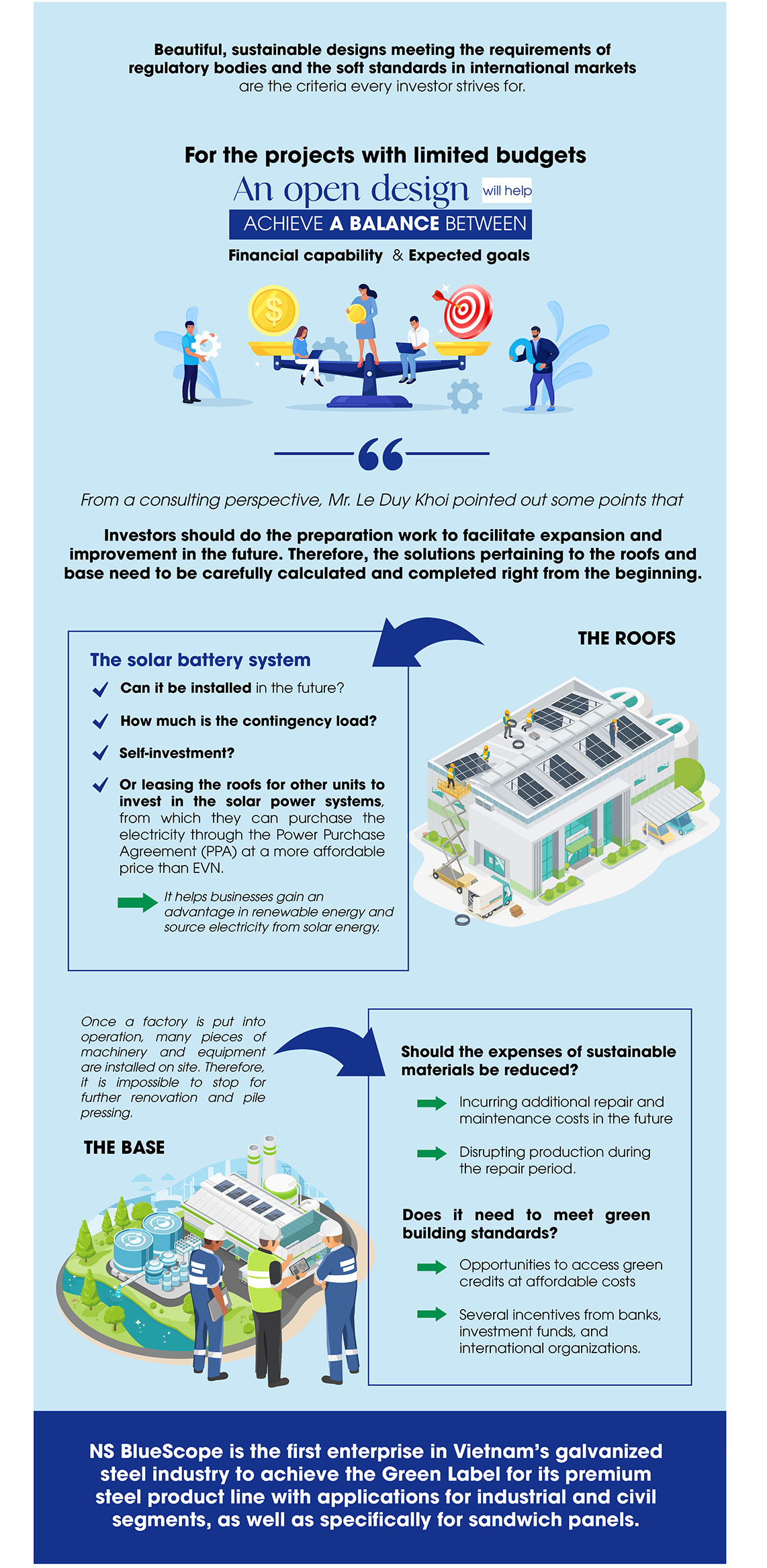
For example, although there is not enough budget to install a solar battery system at present, it is essential to calculate how to install the system on the factory roofs in the future. In addition, it is impossible for the factory to suspend operations to renovate the roofs in the future. Therefore, the roofing solutions should be completed right from the beginning, along with contingencies for the load of the solar battery system in the future.
Besides self-investment in solar power systems, factories can also consider leasing the roofs for other units to invest in the solar power systems, from which they can purchase the electricity through the Power Purchase Agreement (PPA) at a more affordable price than EVN. PPA has become increasingly popular as it helps businesses gain an advantage in renewable energy and source electricity from solar energy.
It is the same for the base. Once a factory is put into operation, many pieces of machinery and equipment are installed on site. Therefore, it is impossible to stop for further renovation and pile pressing. Solutions related to the base should be carefully calculated and completed right from the beginning.
In addition, experts highlight that reducing expenses for sustainable materials can lead to the risk of incurring additional repair and maintenance costs in the future, not to mention production disruptions during the repair period. By meeting green building standards, businesses have opportunities to access green credits at affordable costs and several incentives from banks, investment funds, and international organizations.
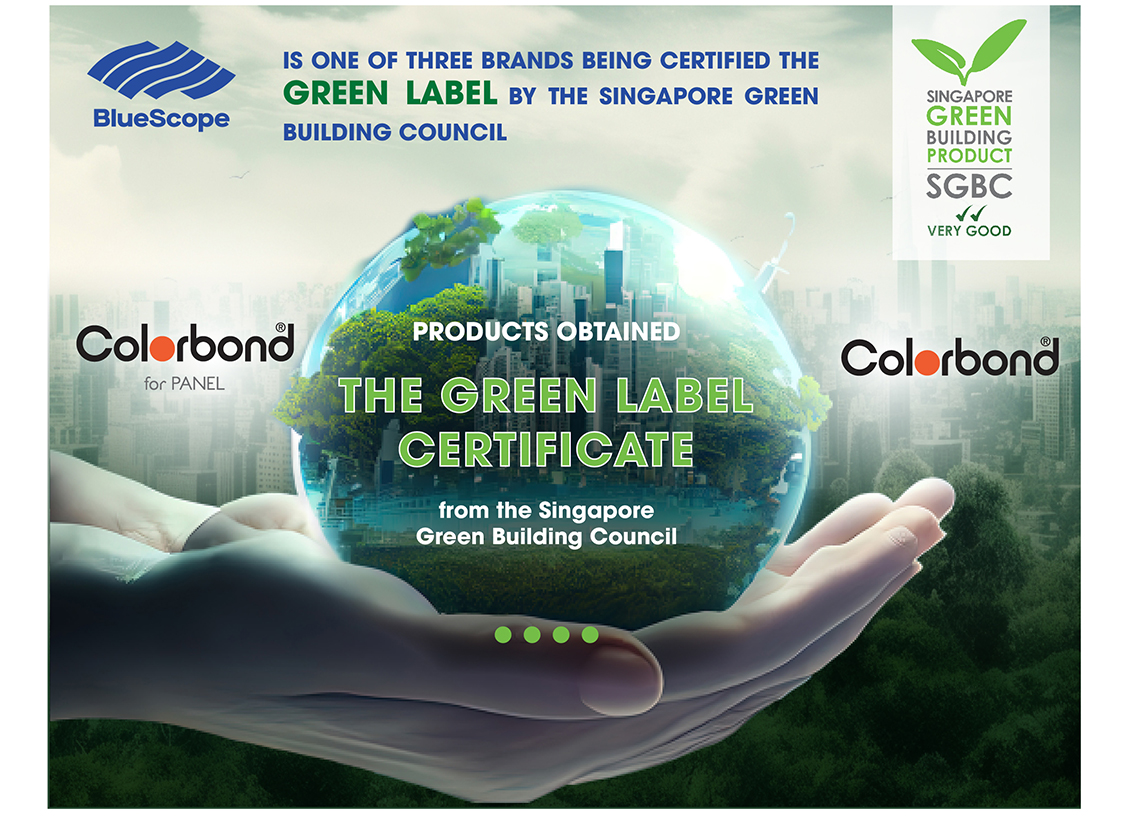
As the leading supplier of steel solutions for construction projects in Vietnam, NS BlueScope’s products are the premier choice for many consulting, design, and green building construction companies.
Among them, COLORBOND® steel is a pre-painted premium product of NS BlueScope Vietnam, produced by a continuous hot-dip metal coating line complying with Australian standards and integrated with ACTIVATE™ technology, which has more than 20 patents globally for its unique four-layer structure.
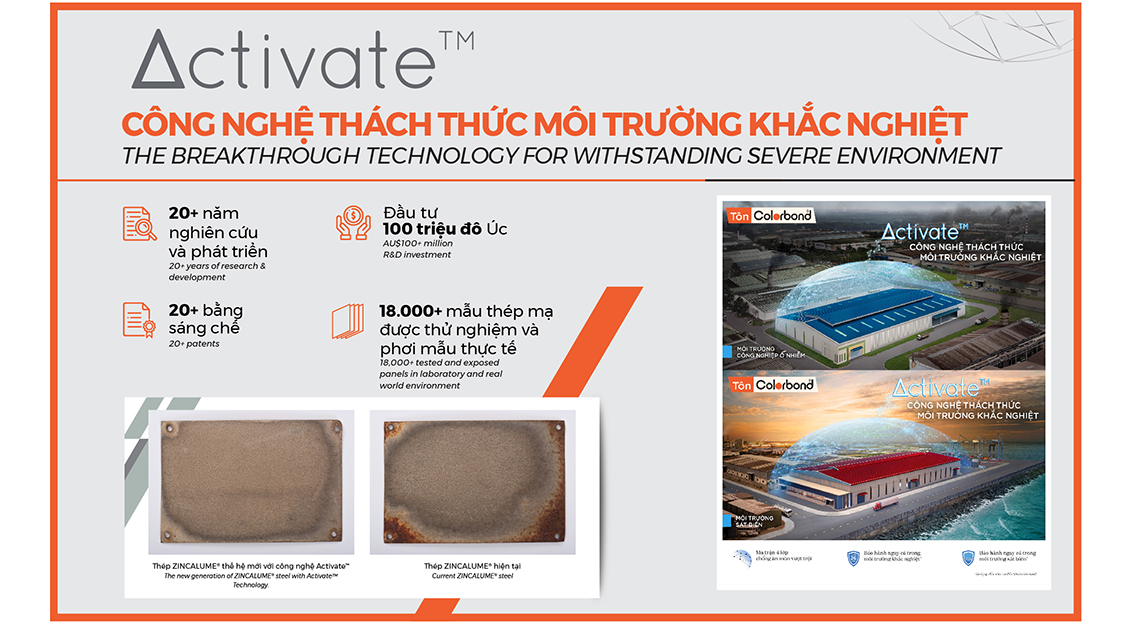
To ensure the COLORBOND® steel with Activate™ technology lives up to the highest expectations in durability, NS BlueScope conducted a comprehensive testing program over a 22-year period. Among them, more than 8,000 profile panels have undergone salt spray testing in laboratories. A further 10,000 panels have been tested at 22 different exposure sites in Australia and around the world. The results were independently verified by the French Corrosion Institute (FCI), proving that COLORBOND® steel is highly durable, especially at the cut edges, and more resilient to scratches and scuffs.
The secret to the superior corrosion resistance of the Activate™ technology lies in the unique composition and microstructure of the 4 phases that create four barriers to protect the steel substrate. With the unique composition and microstructure of the 4 phases, the new generation COLORBOND® and ZINCALUME® steel create a self-sealing effect at cut edges, screw holes, and scratches, thereby providing corrosion resistance for roofs and walls as well as increasing the lifespan of the projects. Activate™ technology shows superior performance to the previous generation after 22 years at Bellambi Point, The Surf Marine Site, Australia. This is an important factor for factories with solar battery systems installed. It is more complicated and expensive to maintain the steel panel below the solar battery system. Therefore, the superior durability and corrosion resistance of COLORBOND® steel will help save a lot of cost and effort for factories.
Comment